With the transom glued into place, the next step is to glue the main stringers to the hull floor and the front support rib. This where I made my first mistake:
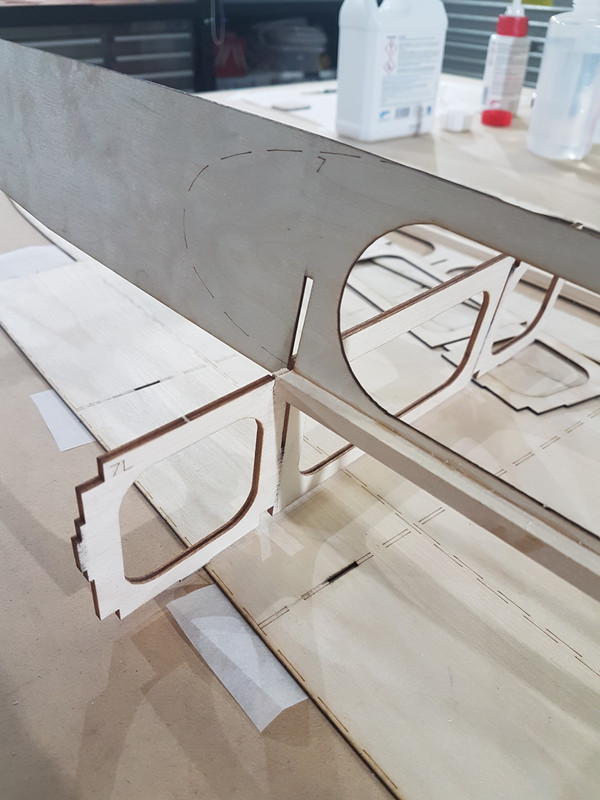
I had glued on the basswood support pieces to the main stringers before affixing to the hull. Unfortunately the main stringers and the ribs slot together to make a very solid and clever design. This means the basswood support pieces get in the way of the slot so you cant join the two pieces together. If you are building put the basswood on last, not first : ) I was eventually able to very carefully bend the wood to make it work without the whole thing coming apart.
Setting up for gluing down the main stringers is one of the more complex glue ups of the build. You need to ensure the stringers are dead straight, and in place at exactly 90 degrees to the hull. The whole thing also needs to be weighed down so its perfectly flat along the whole length. I ended up cutting up some aluminum angle to use as a support for the stringers. On the outside of the hull I actually screwed the angle into the MDF baseboard and then clamped the angle firmly to the stingers.
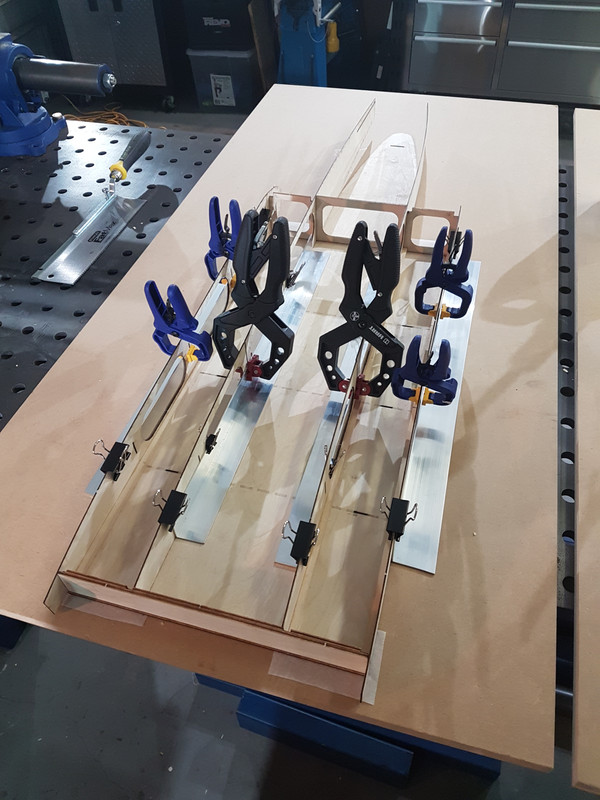
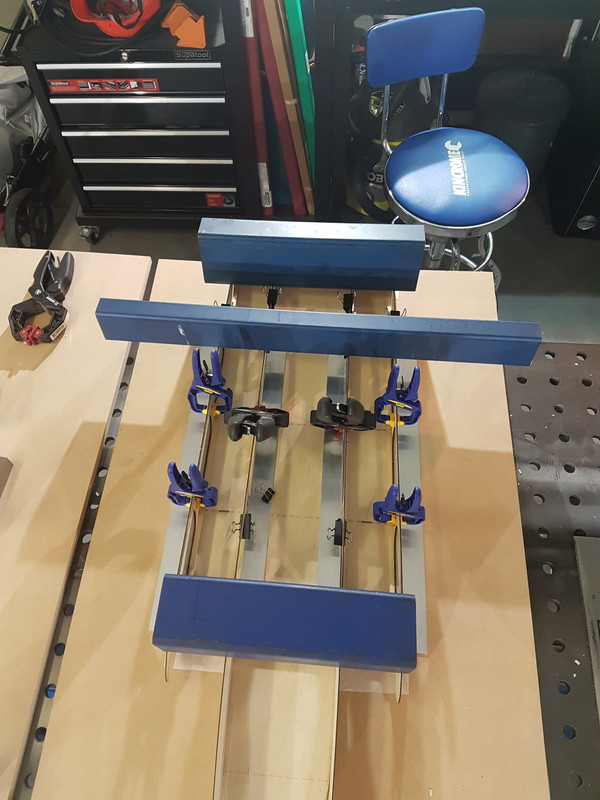
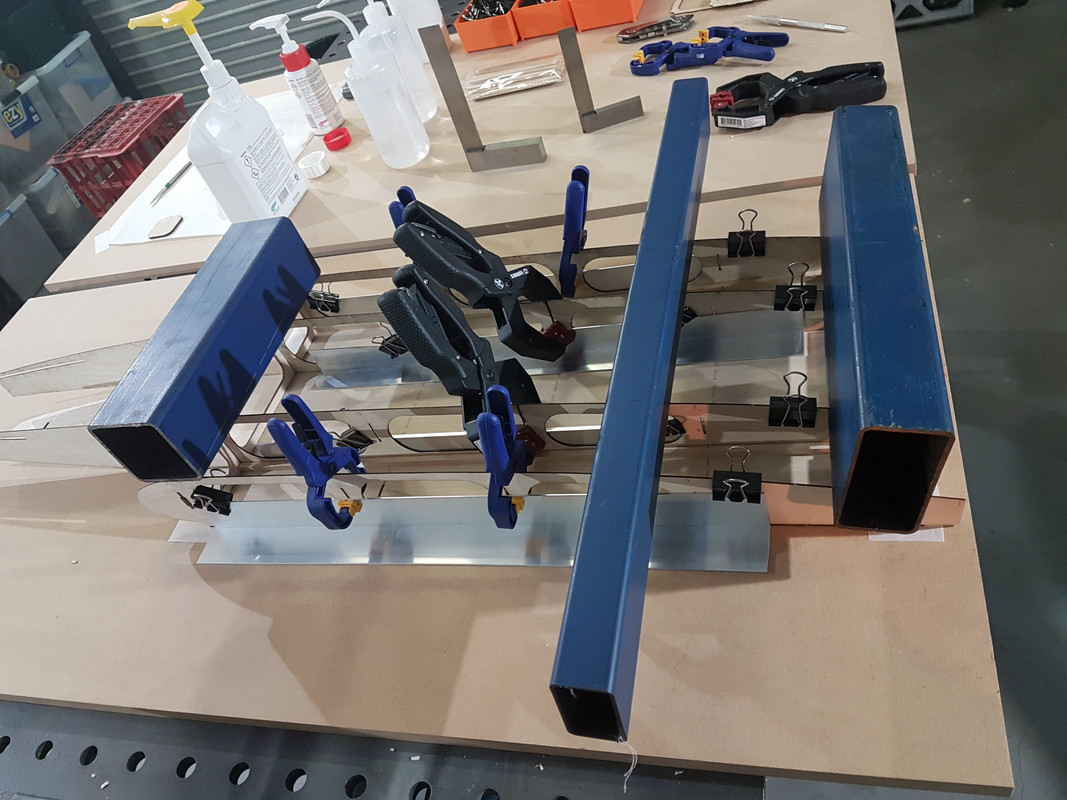
After a full night curing i was able to remove the clamps. Came out dead straight
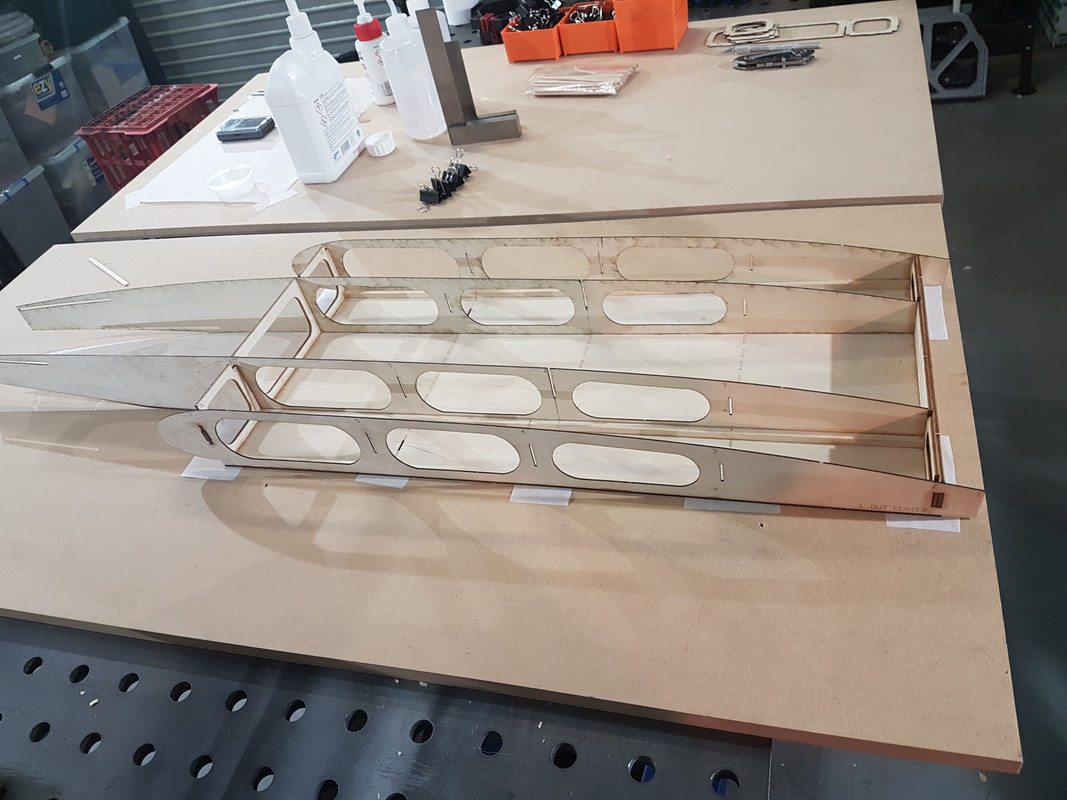
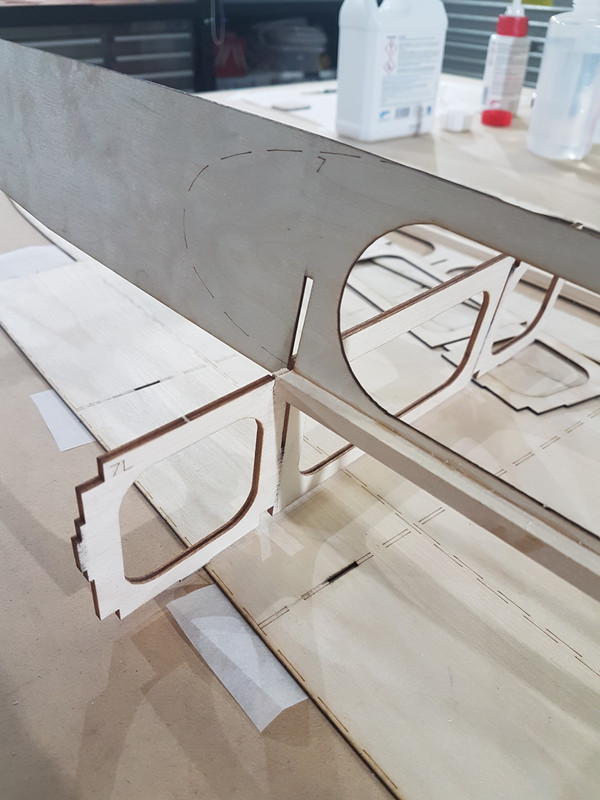
I had glued on the basswood support pieces to the main stringers before affixing to the hull. Unfortunately the main stringers and the ribs slot together to make a very solid and clever design. This means the basswood support pieces get in the way of the slot so you cant join the two pieces together. If you are building put the basswood on last, not first : ) I was eventually able to very carefully bend the wood to make it work without the whole thing coming apart.
Setting up for gluing down the main stringers is one of the more complex glue ups of the build. You need to ensure the stringers are dead straight, and in place at exactly 90 degrees to the hull. The whole thing also needs to be weighed down so its perfectly flat along the whole length. I ended up cutting up some aluminum angle to use as a support for the stringers. On the outside of the hull I actually screwed the angle into the MDF baseboard and then clamped the angle firmly to the stingers.
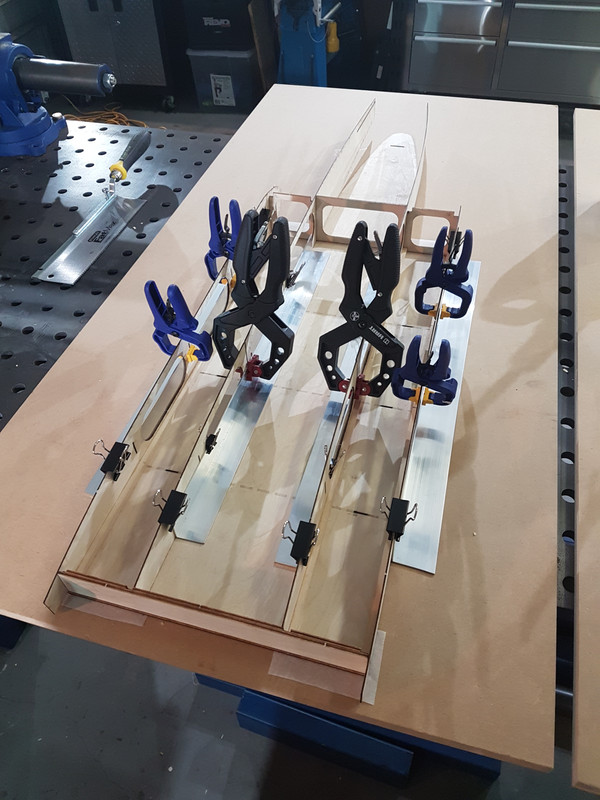
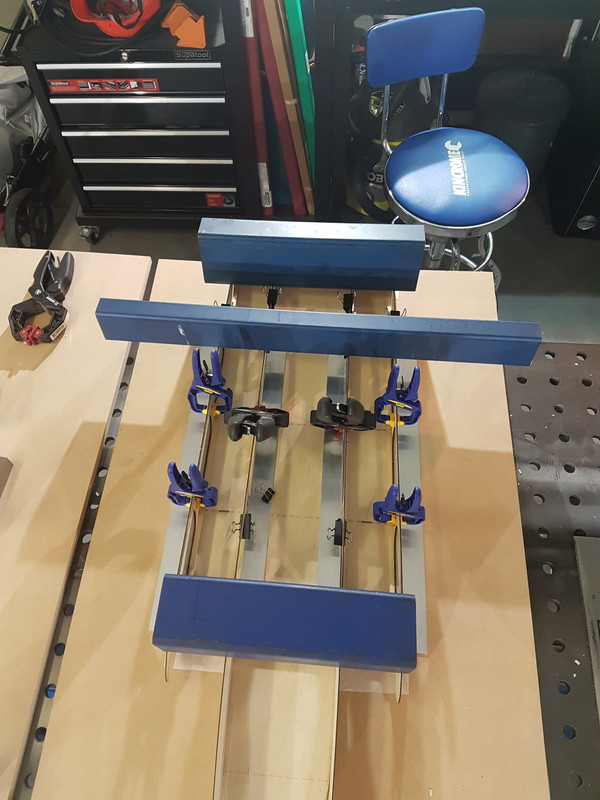
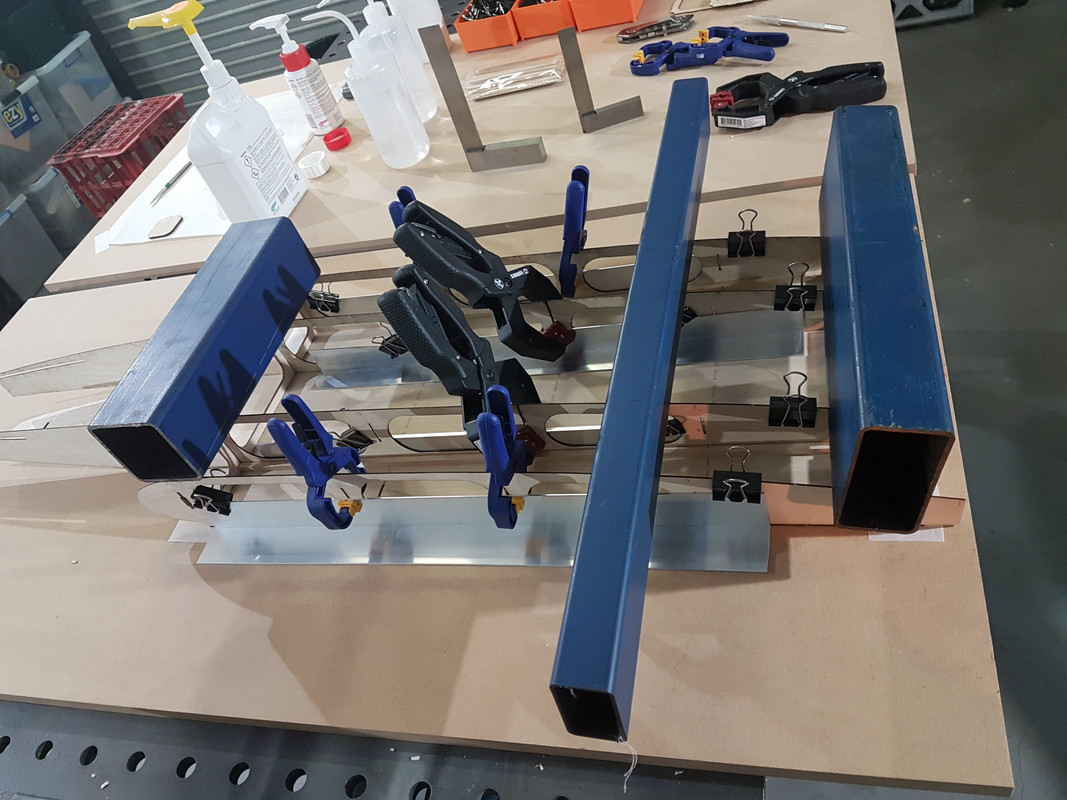
After a full night curing i was able to remove the clamps. Came out dead straight
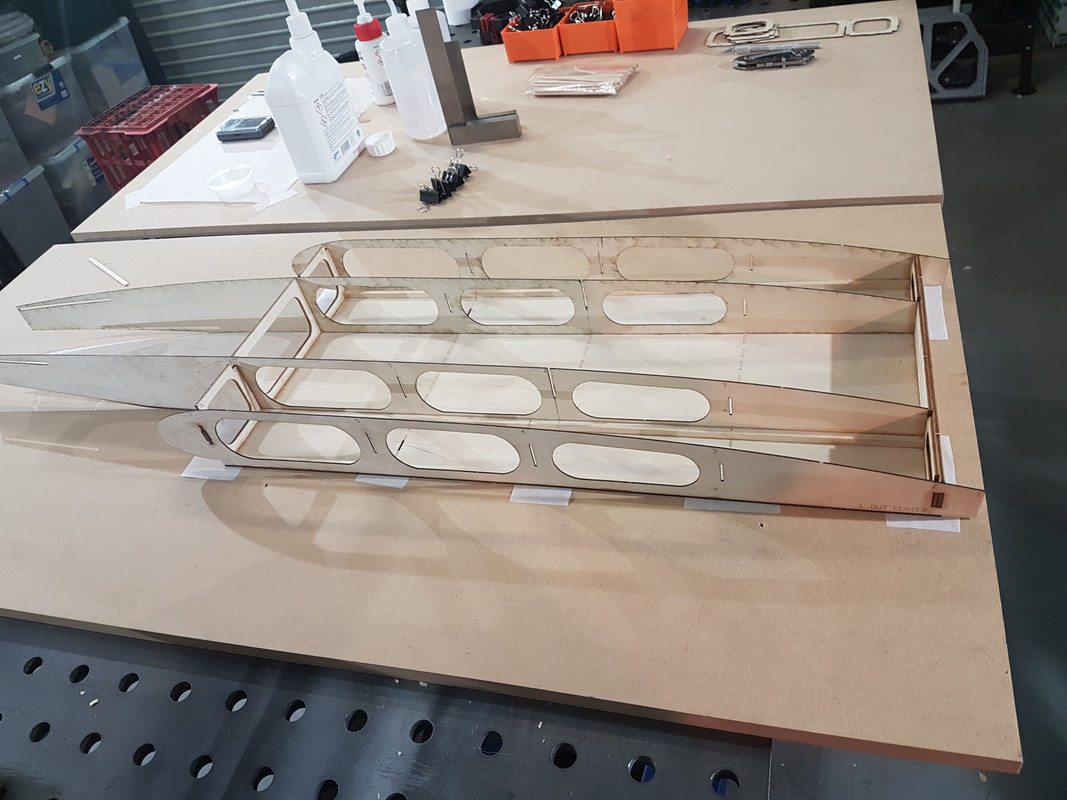
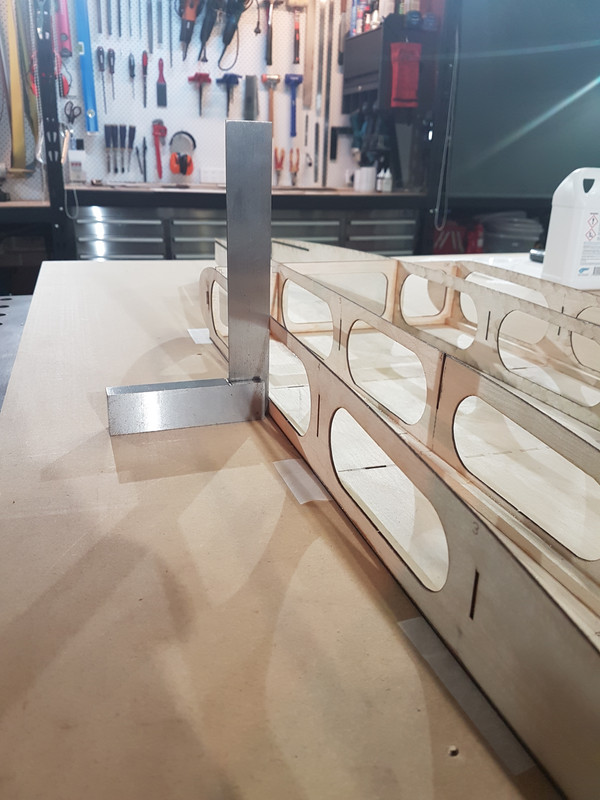
Comment