785boats's 2nd photo is of one of my boats, for clarification the hole at the back and the ones down the side are to let water in, the ones in the steps and the one in the bow is to let the air out, you don't need much area of holes to let the air out (especially for fun running as it doesn't matter how fast it rights), but you do need them, and they have to be on top when the boat is floating upside down.
Hole size matters to some extent, bigger is better especially for the water inlets and I would suggest no smaller than 6mm / 1/4" for an inlet hole, and 3mm / 1/8" for an air outlet. The shape doesn't matter, circles are easy to drill, but if you want to get fancy it wont cause any problems, here is another of my boats, you can see 2 small air outlets drilled in the bottom of the hull through the Ohm symbol on the top deck.
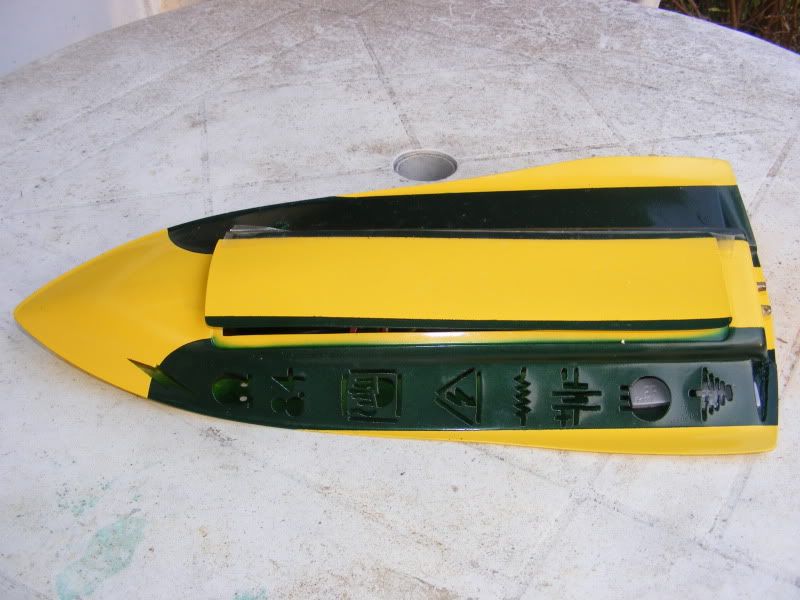
Usually when self-righting monos have 2 packs they will both be on the chamber side, which would probably get rid of at least one of your water bottles.
Hole size matters to some extent, bigger is better especially for the water inlets and I would suggest no smaller than 6mm / 1/4" for an inlet hole, and 3mm / 1/8" for an air outlet. The shape doesn't matter, circles are easy to drill, but if you want to get fancy it wont cause any problems, here is another of my boats, you can see 2 small air outlets drilled in the bottom of the hull through the Ohm symbol on the top deck.
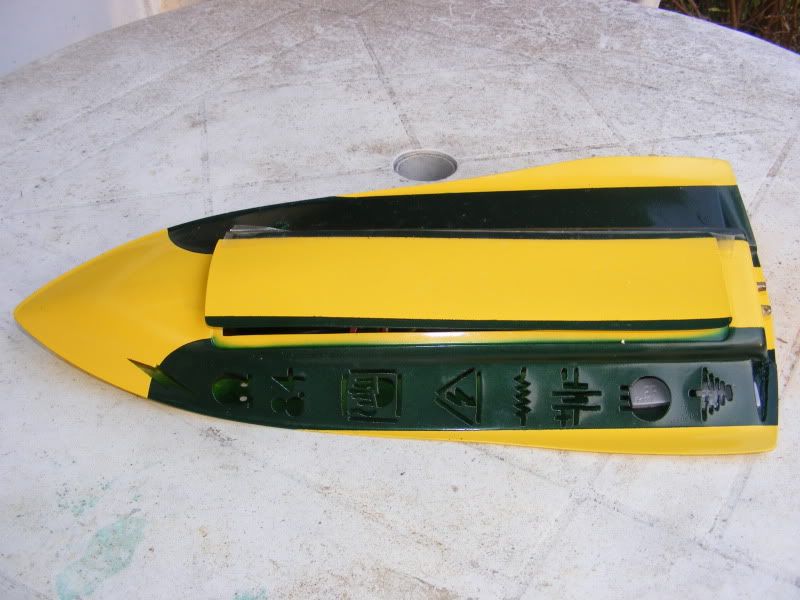
Usually when self-righting monos have 2 packs they will both be on the chamber side, which would probably get rid of at least one of your water bottles.
Comment